Epoxy vs Polyaspartic Concrete Coatings: Curing Time and Durability
February 26th, 2024 | 5 min. read
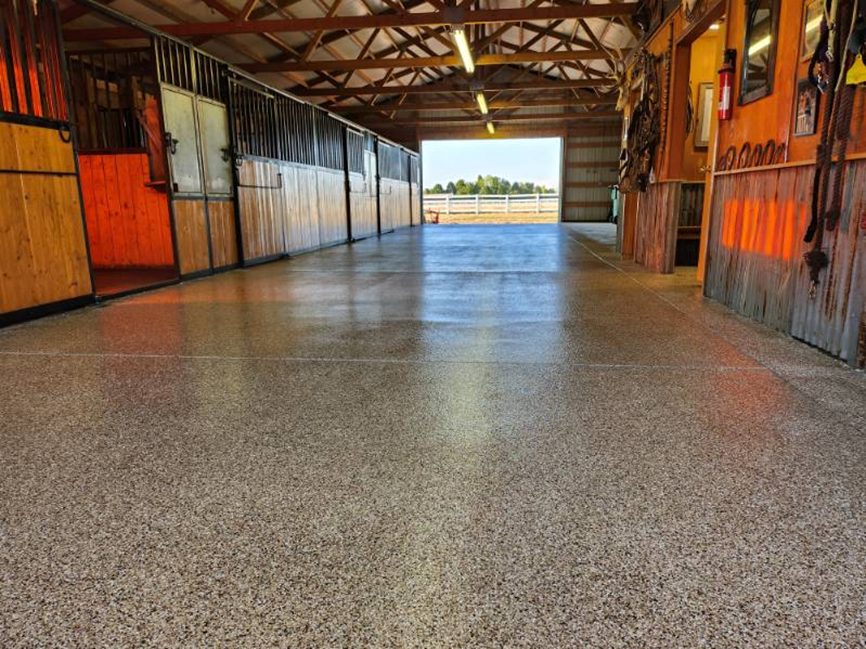
Concrete coatings play a crucial role in protecting and enhancing the durability of floors. Two popular options in this realm are polyaspartic and epoxy coatings. We at Floor Shield utilize a 100% polyaspartic coating for most of our jobs, but we also sell a whole line of epoxies. Polyaspartic flooring installers offer distinct advantages over epoxy floor coating businesses.
When considering both options for your concrete, you may be wondering, “What are the differences between polyaspartic and epoxy coatings?” and “Which one is better for my specific situation?”
We’ll answer both questions honestly and do our best to cover all the bases so you have a holistic look at the pros and cons of both.
Chemical Composition
Epoxy Coatings:
Epoxy coatings consist of epoxy resins and hardeners. When these components are mixed, a chemical reaction occurs, resulting in a rigid and durable surface. Epoxy coatings are known for their excellent adhesion to concrete, forming a strong bond with the floor.
Polyaspartic Coatings:
Polyaspartic coatings, on the other hand, are based on aliphatic polyurea technology. These coatings result from a reaction with a polyaspartic ester, creating a flexible and robust surface. Polyaspartic coatings also exhibit strong adhesion to concrete surfaces.
Preparing the Surface
If your floor is suffering from hairline cracks and/or spalling, the natural curing process of epoxy and polyaspartic coatings will usually level the floor out and hide damages to a degree. However, you want an installation crew to ensure your floor is optimally leveled so that you don’t have any adhesion issues down the road. To do this, your installer should grind and sand the concrete, which will give your concrete floor a suitable profile that a coating can easily adhere to.
Both polyaspartic and epoxy coatings will have trouble sticking to a surface that is not well-textured. When a coating has adhesion issues, it’ll peel off your floor easily.
Curing Time
Epoxy Coatings:
Epoxy coatings have a considerably longer curing time than polyaspartics. The drying process may take several days (usually two), and factors such as temperature and humidity can influence the duration. While they offer a durable finish, the extended curing time can be a limitation in projects with tight timelines where you need to re-access the space ASAP.
Polyaspartic Coatings
Polyaspartic coatings are renowned for their rapid curing time. Unlike epoxy coatings, which will take days to dry, polyaspartic coatings can dry within a few hours (in the 4 – 6 range), which even surpasses polyurea coatings that boast a dry time of about 6 – 8 hours. This characteristic makes them an excellent choice for projects that require a quick turnaround.
Application Temperature
Epoxy Coatings:
Epoxy coatings have temperature limitations during application. Extreme temperatures can impact the curing process and the final result. Very low or high temperatures will interrupt the epoxy curing process. In cold weather especially, the curing process will be slowed, and at a certain temperature, it won’t cure at all.
If you want your concrete coating to cure in the usual timeframe, it should be at least 50 degrees Fahrenheit before you install the epoxy. It's essential to always consider environmental conditions when installing any concrete coating.
Polyaspartic Coatings:
Polyaspartic coatings offer greater versatility in terms of application temperature. They can be applied in a broader range of temperatures, including colder environments below freezing.
When it’s very cold, the only concern is maintaining the product’s viscosity. This can be circumvented by keeping the material in a space at room temperature before application. The application flexibility of polyaspartics makes them suitable for various climates and seasons.
UV Stability
In the United States, 95% of garages get direct sunlight in the first 12 to 18 inches. This is why it is so important to get a coating that is resistant to damage from the sun, as fading and yellowing on one part of your garage coating will create an ugly inconsistency.
Epoxy Coatings:
One potential drawback of epoxy coatings is their susceptibility to yellowing or degradation when exposed to UV radiation over time. Additional topcoats will be required for UV protection on outdoor applications. However, these usually come in the form of protective clearcoats, which while do offer resistance against solar damage, are not going to prevent noticeable damage even after just the first few years.
Polyaspartic Coatings:
Polyaspartic coatings excel in UV stability. They are much less prone to yellowing or degradation when exposed to sunlight. This makes them a preferable choice for outdoor surfaces that are subject to constant sun exposure.
Floor Shield, our 100% polyaspartic concrete coating, is test-proven to be completely UV stable. When we tested Floor Shield against a polyurea/polyaspartic coating blend—which is more UV stable than an epoxy—our coating saw no change after spending 1000 hours under a QUV lamp, while the competitor yellowed significantly.
Flexibility
Epoxy Coatings:
Epoxy coatings are generally rigid and hard. While they provide a durable surface, they may lack the flexibility required to withstand the natural movement of the ground. This makes them more prone to cracking and breaking off the substrate than polyaspartic coatings.
Polyaspartic Coatings:
Polyaspartic coatings exhibit greater flexibility, giving them resistance to cracking. This makes them a great option if you don’t want to worry about having to repair cracks regularly. This flexibility contributes to their resilience in various applications.
Adhesion
Epoxy Coatings:
Epoxy coatings are known for their strong adhesion to concrete surfaces. This reliable bond ensures a durable and long-lasting finish, particularly in high-traffic areas.
Polyaspartic Coatings:
Polyaspartic coatings also boast excellent adhesion to concrete. The strong bond they form contributes to the longevity and performance of the coating, making them a reliable choice.
Chemical Resistance
Epoxy Coatings:
Thanks to their strong chemical resistance, epoxy coatings provide effective protection against a variety of chemicals commonly present in industrial settings. There are also several variants of epoxies that are made to be extremely robust against chemicals.
Polyaspartic Coatings:
Polyaspartics are generally just as much if not more chemically resistant than epoxies. However, there are several types of epoxies that specialize in chemical resistance, which beat out most polyaspartics.
Durability and Longevity
Epoxies are less durable and are quicker to break down than polyaspartics. Many epoxies will utilize a urethane-based topcoat, which is less durable than a polyaspartic. Many polyurea applications will even use a polyaspartic topcoat because they are the more durable coating option in general.
When we tested Floor Shield against a polyurea coating, which is more durable than a traditional epoxy, the result showed Floor Shield as the stronger option.
Yet, in situations requiring the application of multiple, thick coatings—such as areas with regular heavy machinery and vehicle traffic—epoxy stands as the sole viable choice. Unlike polyaspartics, which struggle to adhere properly when coated too thick, epoxies exhibit no issues.
Project Considerations
When deciding between polyaspartic and epoxy coatings, it's crucial to consider the specific requirements of the project.
Time Sensitivity: For projects with tight timelines, polyaspartic coatings offer a significant advantage due to their rapid curing time.
Industrial Settings w/ Heavy Machinery: Since epoxies can be applied in thicker layers than polyaspartics, they might be better for floors that need to hold heavy machinery.
Outdoor Applications: If your floor is exposed to the sun, polyaspartic coatings are preferable for their UV stability.
Indoor Applications: Since UV radiation won’t be a factor, and because there are so many cheap DIY epoxies that you can find in many retail stores, epoxy is a good choice if you have a smaller space indoors that you want a coating on. While we recommend going with a professional in any installation situation, if you want to do the work yourself, epoxies are the more cost-effective choice.
Investment Consideration: On average, polyaspartic coatings last much longer than epoxies. So, while you will probably pay more for a polyaspartic coating initially, the long-term investment will mean you save more in the long run, as you won’t have to recoat your floor nearly as often.
Flexibility Needs: For areas where substrate movement is a concern, polyaspartic coatings, with their enhanced flexibility, are the optimal choice.
Both polyaspartic and epoxy coatings have their pros and cons, and your pick should depend on the specific needs of your project. Whether prioritizing curing time, UV stability, flexibility, or adhesion, each coating type has its unique advantages in various applications.
If you are interested in Floor Shield’s 100% polyaspartic coating, scroll down.